PACKAGING DEVELOPMENT
Experts for pharmaceutical barrier packaging
Our pharmaceutical packaging experts develop, optimize, analyze and test packaging with the aim of optimizing barrier properties and thus ensuring the stability of your products.
We focus on:
- Barrier and Shelf Life
- Analytical methods and benchmarking
- Packaging validation and performance testing
- Damage and problem analysis
We offer comprehensive know-how for pharmaceutical packaging:
- Thermoformed and cold-formed blisters (thermoforming and coldforming)
- stick packs
- pouches
- bottles
- Injection vials / vials
- Syringes
Our range of services extends from standardized testing to unconventional analysis methods. Benefit from our history as a former research center of a global corporation and place your trust in our exceptional material know-how, our great expertise and our first-class laboratory infrastructure.
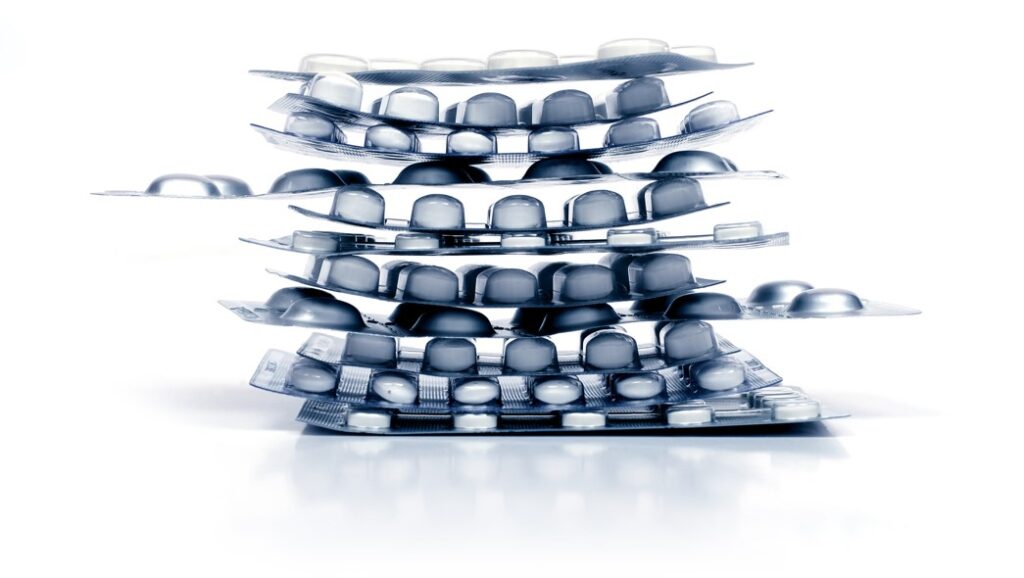
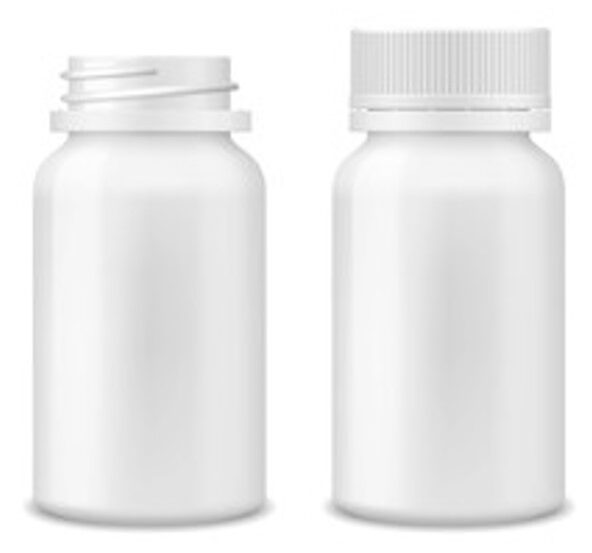
Packaging development
Progress through material expertise
The demands placed on pharmaceutical packaging are varied and high. The packaging, which is mainly made of plastic and aluminum, must meet high functional requirements, for example in terms of barrier, sealability or formability. In addition, increasingly stringent requirements apply with regard to recyclability and the absence of halogens such as chlorine or fluorine.
The high requirements often conflict with material and cost reduction. Consequently, the physical and mechanical properties of materials should be exploited to the full. This requires a sound and comprehensive understanding of materials.
As an independent service provider, Suisse Technology Partners AG is a long-standing partner of the pharmaceutical industry and supports its customers in packaging development, product and process optimization or in the event of damage (damage analysis).
Barrier and shelf life
In order to guarantee the functionality and shelf life of pharmaceutical products, the contents must be protected from external influences such as moisture or oxygen and the effects of temperature.
The barrier of both thermoformed and cold-formed blisters can be determined using numerical simulation and specifically developed analytical calculation methods.
BARRIER CALCULATION OF THERMOFORMED BLISTERS
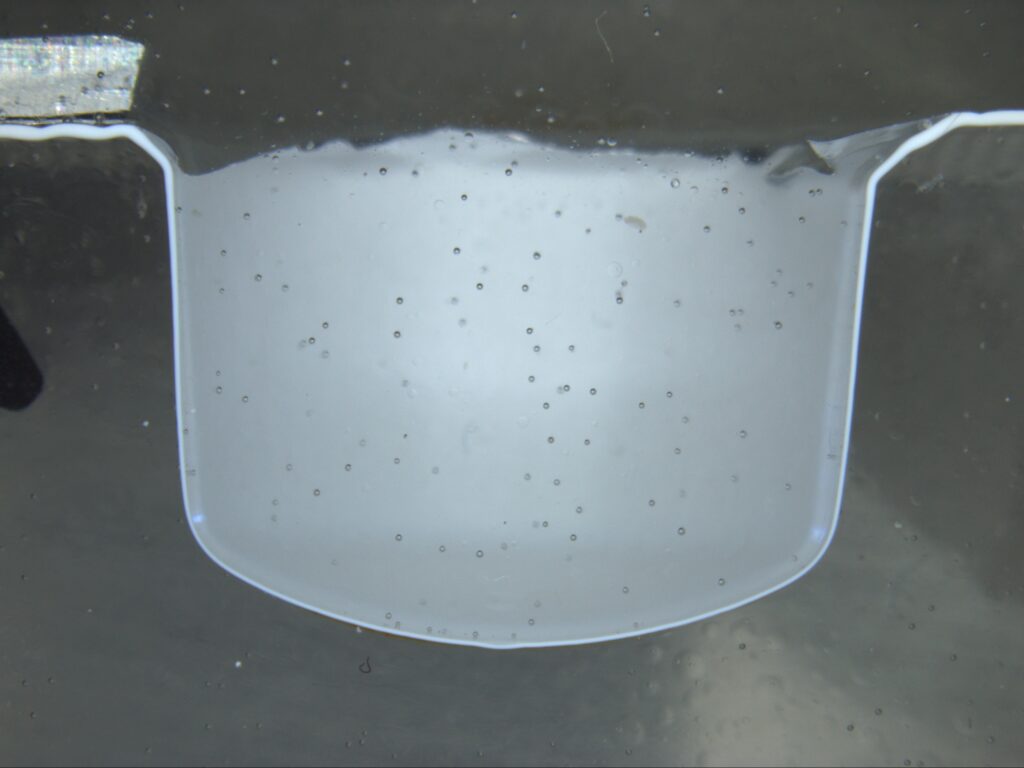
Analytical barrier calculation (WVTR, OXTR) based on thickness measurements on existing blisters
Numerical barrier calculation (WVTR, OXTR) using FEM (finite element method).
In thermoformed blisters, the forming process has a direct impact on the barrier properties of the packaging and consequently on the shelf life of the product. By using numerical simulation methods, predictions can be made without having to invest in expensive forming tools.
The material properties required for this are determined in specially developed test procedures in our own laboratories.
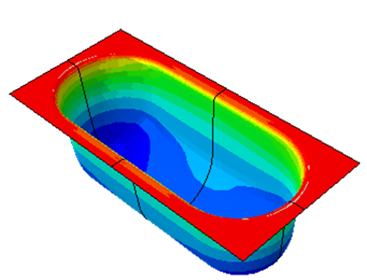
BARRIER CALCULATION OF COLD-FORMED BLISTERS (CROSS-DIFFUSION)
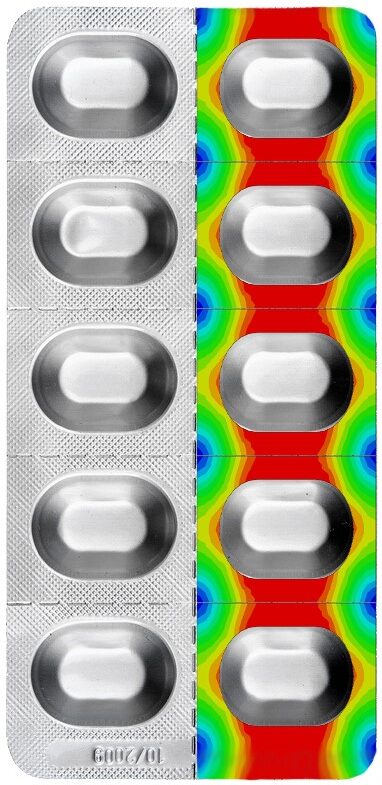
Although aluminum is considered a 100 percent barrier against water vapor and oxygen, moisture can penetrate through the sealing layer of an aluminum blister and damage the product or reduce its service life. This so-called cross diffusion can only be measured on a blister with relatively great effort. However, Suisse Technology Partners has developed a method for predicting cross diffusion by computer simulation.
The material properties required for this are determined in a specially developed test procedure.
In addition, the moisture absorption (LOD: loss on drying) or shelf life of the filling material can be calculated taking into account its sorption properties.
SHELF-LIFE PREDICTION
Based on the barrier of the packaging and taking into account the physical properties of the product, it is possible to directly predict its shelf life. This means that complex stability tests can be shortened or even completely replaced.
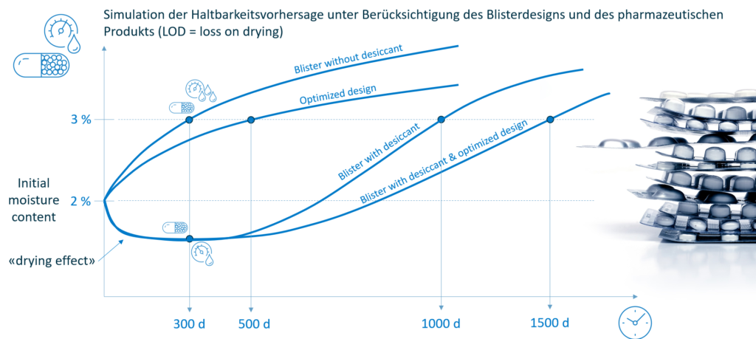
THERMAL IMPACT ANALYSIS
Numerical simulation is used to calculate the thermal influence of the sealing process on the product. This makes it possible to determine possible degeneration of the product due to heat input during the normal process, but also in particular during unforeseen processes such as production interruptions.
- Prediction of the time-dependent temperature distribution in the blister
- Investigation of general heat transfer issues
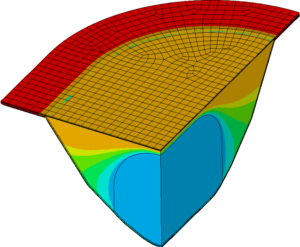
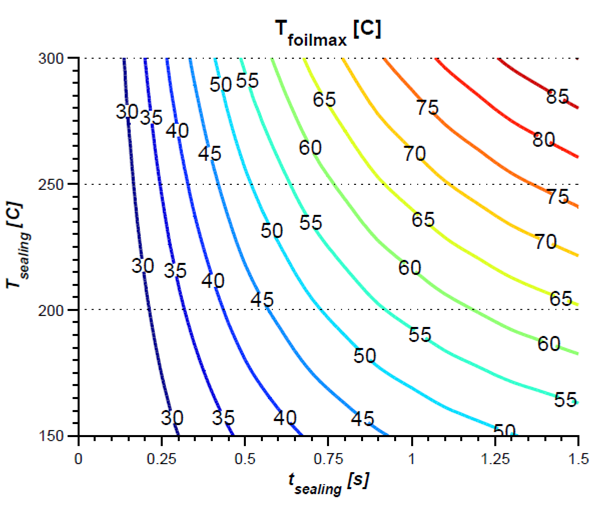
Analytical methods
A variety of methods are available for analyzing packaging during the development process, in the event of damage or as part of quality assurance.
In addition to optical testing using light microscopy, scanning electron microscopy (SEM/EDX) and many other materialographic, physical and chemical testing options are also available.
The variety of analysis methods, coupled with the many years of experience of the experts at Suisse Technology Partners, enable successful support for complex issues.
BENCHMARKING OF PACKAGING FILMS AND PACKAGING
As an independent service provider, we characterize and compare the structure, material composition and performance etc. of packaging films (semi-finished products) or packaging using suitable analysis methods.
Multi-layer analysis of a thermoformed barrier blister
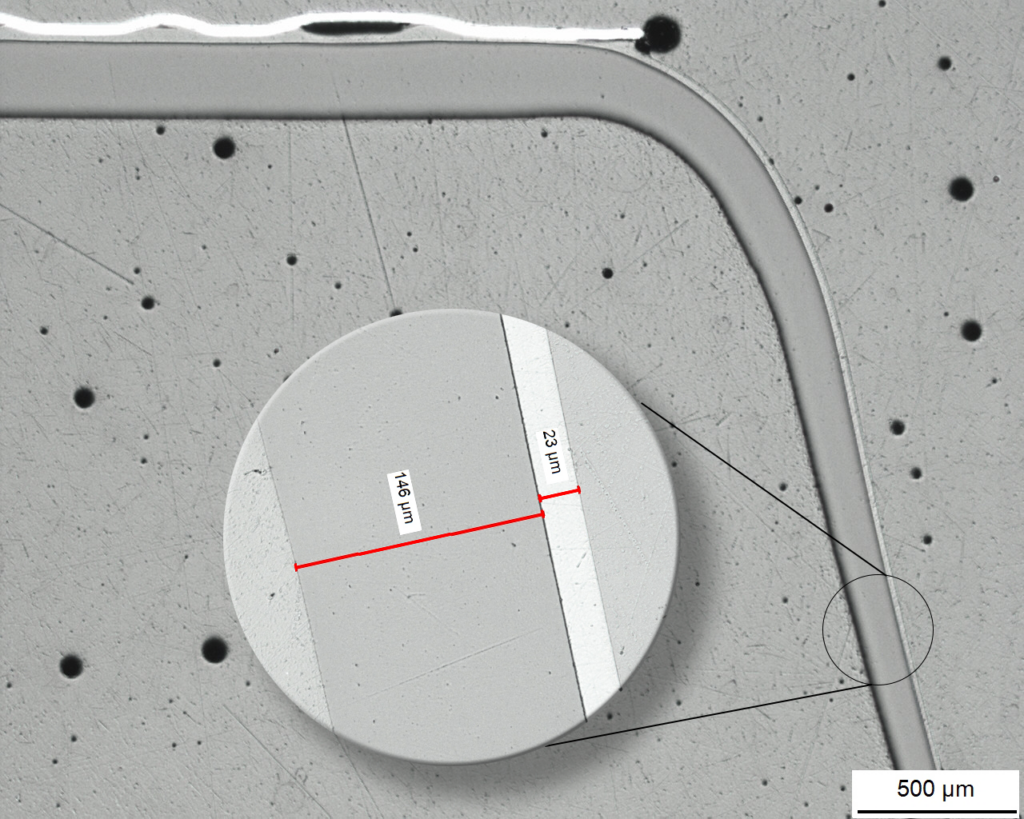
Micrograph of a cavity
The layer structure is visualized and measured on the metallographic cross-section under the microscope.
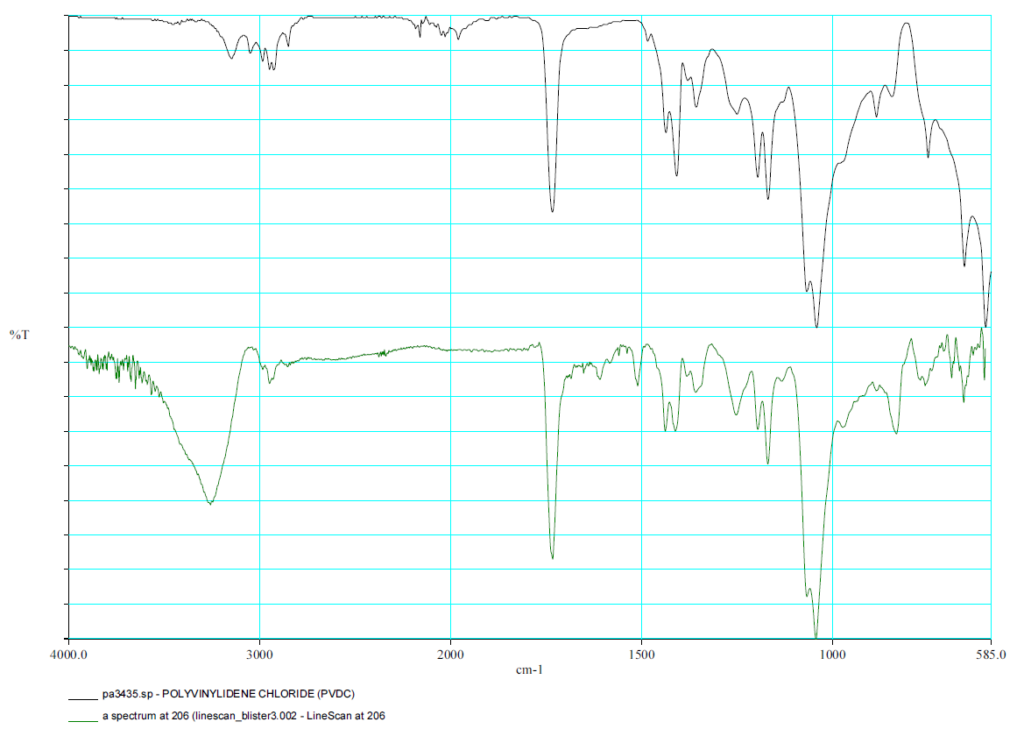
FTIR Spectrum PVDC
The individual layers are analyzed using an FTIR microscope.
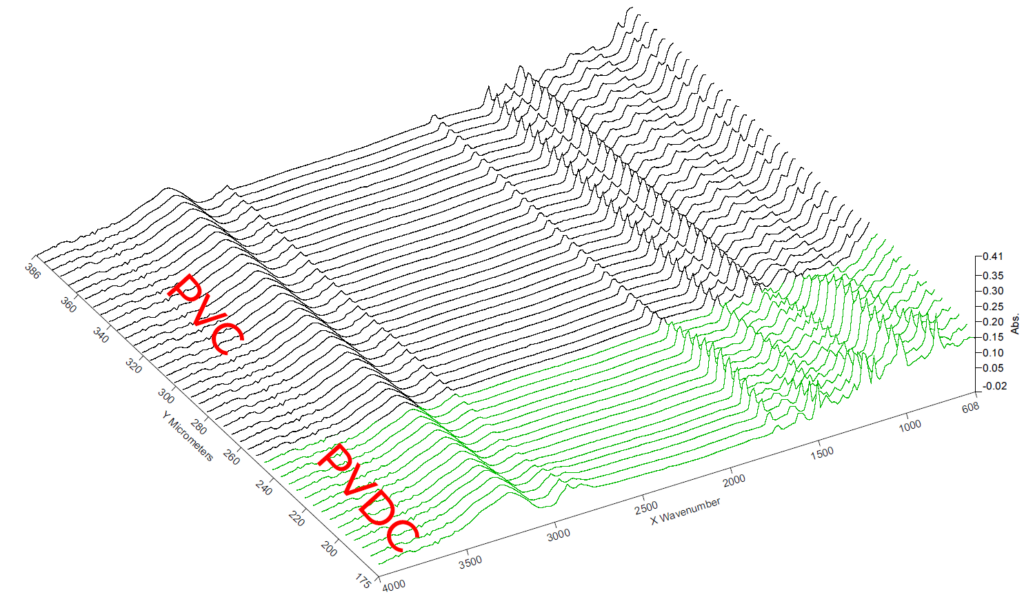
FTIR - Linescan
In the linescan, the spectra of the materials are displayed over the structure.
Forming Limit Analyse
Optical strain measurement is used to evaluate the forming conditions and surface strains of aluminum-aluminum (coldform) blisters.
The forming limit diagram (FLD) shows the tendency to crack formation based on the strain measurement and the formability of the material (forming limit curve, FLC). This can be used as a measure of process stability.
PACKAGING VALIDATION AND PERFORMANCE TESTING
We support you in the validation of packaging and packaging processes. We carry out both standardized and customer-specific tests in our extensive laboratories:
- Leak tests (e.g. dye leak test)
- Sealing seam integrity, sealing seam tightness
- Sealed seam strength (ASTM F88, accredited method)
- Analytical examination of the seal seam using 3D computed tomography CT, microscopy or REM with EDX
- Thickness measurement on films and packaging
- Accelerated ageing, climate and UV tests
- Mechanical and physical tests
- Damage and problem analysis
- Polymer technology and chemical investigations (infrared spectroscopy FTIR with FTIR microscope, TGA, DSC, DMA, TMA, rheometer, calorimeter, coulometer, water content, etc.).
- Measurement of cross-diffusion (determination of permeation properties)
- WVTR measurement according to USP 671
- Customized tests
DAMAGE AND PROBLEM ANALYSIS
Failure analysis is a systematic procedure for determining the cause of the failure. Find out more at Failure analysis.
Beispiel der Röntgenprüfung der Siegelnaht eines Hochbarriereblisters mittels Kontrastmittel. Undichte Stellen sind auch über grössere Flächen sehr gut erkennbar. Die REM Bilder zeigen die Ausbildung und Qualität der Siegelnaht mit sehr hoher Auflösung.
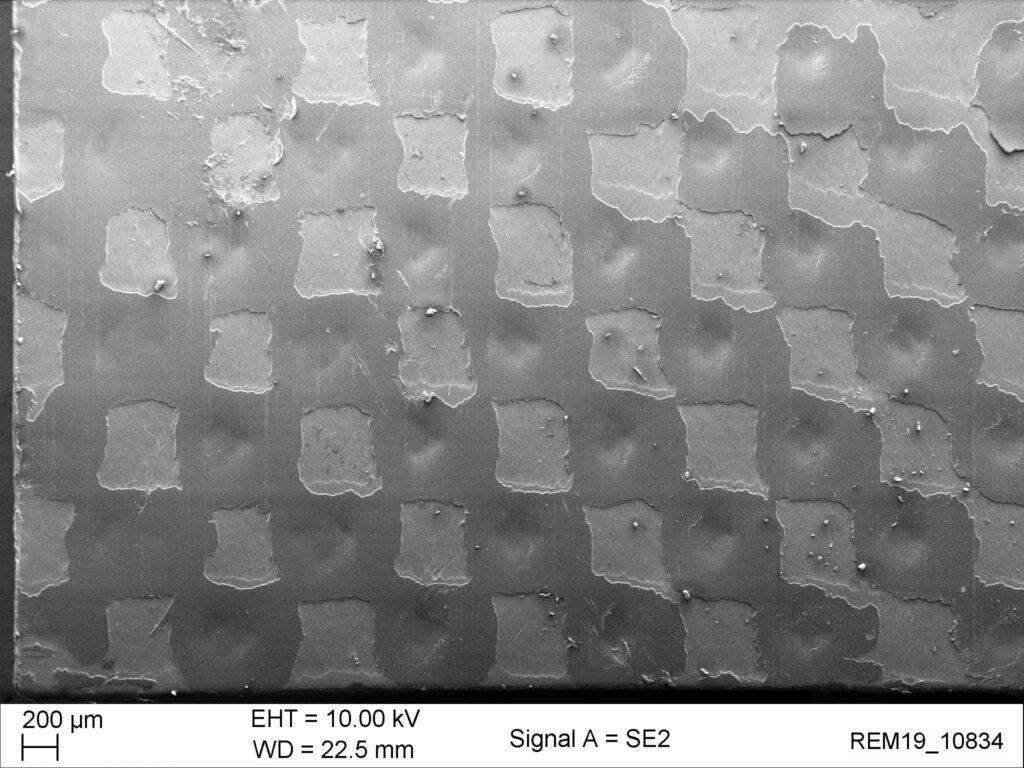
intakte Siegelung
Bei einer intakten Siegelnaht verbinden sich die Klebepunkte so, dass eine geschlossenporige Siegelfläche entsteht.
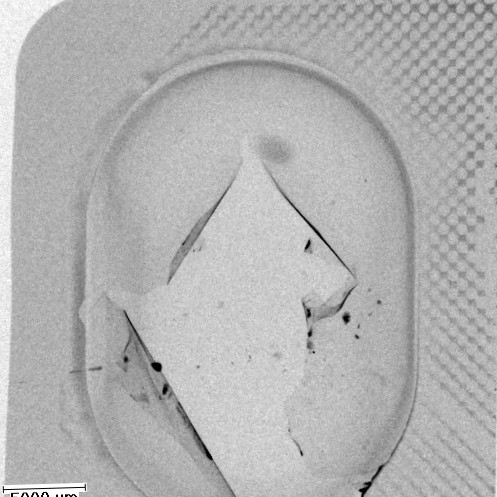
2D - CT Aufnahme mit Kontrastmittel
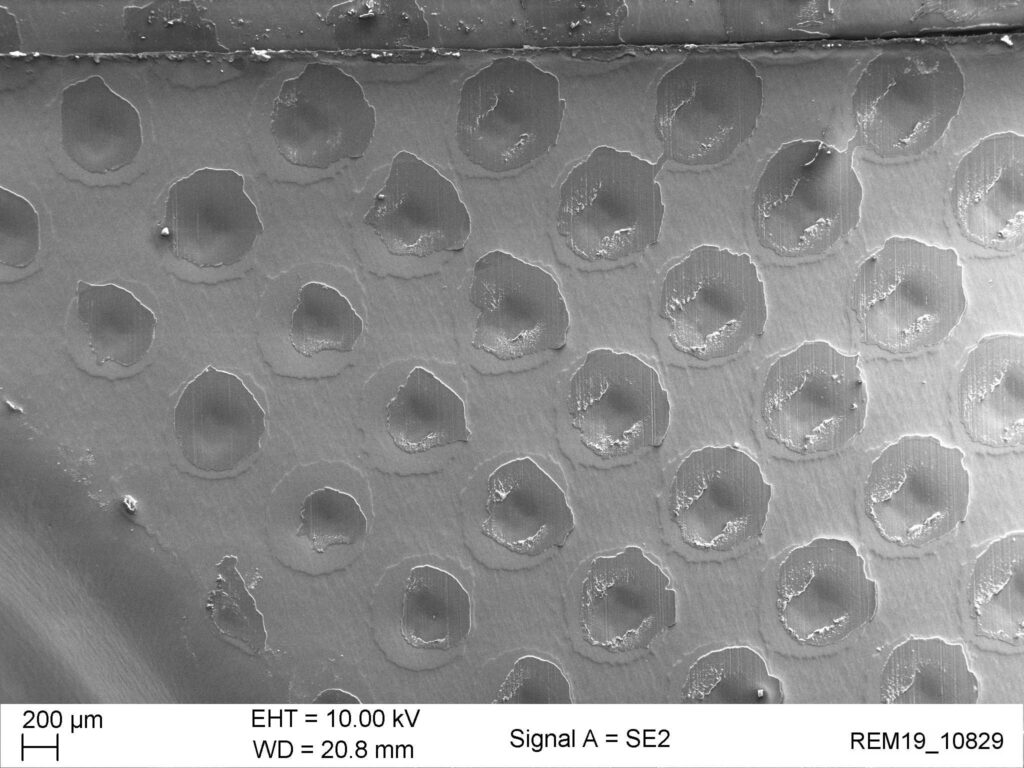