Characterization of aluminium surfaces
We compare surfaces by characterizing their properties.
In order to be able to develop and optimize surfaces, we describe surfaces quantitatively and qualitatively. This also enables us to compare them with a specification or an existing product.
Standards and test methods at Suisse TP
Our service laboratory for aluminum surfaces offers a wide range of tests to ensure that your coatings meet the required standards and requirements.
The removal test according to DIN EN ISO 3210 / ASTM B680 / ASTM B137 is a test method used to evaluate the quality of surface coatings. This test method is particularly relevant for anodized coatings, as the quality of these coatings depends heavily on the compaction of the anodized pores.
As part of the removal test, the test specimen is immersed in an acid solution and left for a defined period of time. The acid solution removes the surface coating and the resulting mass loss is measured. The higher the removal in the acid, the lower the quality of the coating.
The removal test is an important test for assessing the quality of surface coatings and ensuring that they meet the required standards and requirements.
Resistance tests in accordance with DIN EN ISO 2812 and TL 212 are test methods used to evaluate the resistance of coatings to various influences. These tests are widely used in the industry and play an important role in the quality assurance of coatings.
DIN EN ISO 2812 describes various methods for determining the resistance of coatings to chemical substances. For this purpose, the coatings are applied to a test surface and then exposed to various chemicals. The degree of resistance is assessed on the basis of the extent of changes to the coating, such as color changes or coating peeling.
TL 212, also known as the “Bundeswehr test”, is another resistance test that is widely used in the aerospace industry. This test method consists of a cycle of different tests in which the coating is exposed to various influences such as temperature changes, humidity, salt spray and UV radiation. Here too, the degree of resistance is assessed by the extent of the changes to the coating.
Resistance tests according to DIN EN ISO 2812 and TL 212 are important to ensure that coatings meet the requirements and standards in terms of resistance. These tests are an important part of the quality assurance of coatings and help to ensure that coatings provide the required protection and have a long service life.
The pencil hardness test is a simple but effective method for evaluating the hardness and resistance of surface coatings. In this test, a pencil with a defined hardness is applied to the surface of the coating and drawn across the surface with a certain amount of pressure. The hardness of the pencil lead required to penetrate the coating is used as a measure of the hardness of the coating.
Pencil hardness testing is particularly useful for evaluating coatings used in environments with high abrasion or scratching, such as machine components or furniture. By performing this test, we can ensure that your coatings meet the requirements in terms of hardness and resistance.
Our experienced and qualified team of experts carries out pencil hardness testing in accordance with DIN EN ISO 15184 and ASTM D3363 with the utmost care and precision.
The Buchholz hardness test is a simple and effective method for determining the hardness of surface coatings. In this test, a ball pin with a defined diameter is applied to the coating and pressed into the surface with a certain amount of pressure. The diameter of the resulting indentation is measured and used as a measure of the hardness of the coating.
The Buchholz hardness test is particularly useful when evaluating coatings used in high wear environments, such as machine components or in the automotive industry. By carrying out this test, we can ensure that your coatings meet the requirements in terms of hardness and wear resistance.
Our experienced and qualified team of experts carries out the Buchholz hardness test in accordance with DIN EN ISO 2815 with the utmost care and precision.
The mandrel bending test is an important test for evaluating the flexural strength of coatings. In this test, a thin metal pin, also known as a mandrel, is placed on the coating and bent with a defined pressure until the coating cracks or flakes off. The angle at which the coating fails is measured and used as a measure of flexural strength.
The mandrel bending test is particularly useful when evaluating coatings that are exposed to high bending stresses, such as in the production of aluminum profiles or sheets. By carrying out this test, we can ensure that your coatings meet the requirements in terms of flexural strength and load-bearing capacity.
Our experienced and qualified team of experts carries out the mandrel bending test in accordance with DIN EN ISO 1519 with the utmost care and precision.
Color measurement is a precise method for evaluating and comparing the color of coatings and surfaces. In this test, the reflected light from the surface is recorded and converted into spectral color values. The spectral color values are then compared with reference values to detect deviations and evaluate color accuracy.
Color measurement is particularly useful when evaluating coatings used in the printing, automotive or plastics industries. By performing this test, we can ensure that your coatings meet the requirements in terms of color accuracy and color consistency.
Our experienced and qualified team of experts carries out color measurement in accordance with DIN EN ISO 11664-4 with the utmost care and precision.
The color drop test is used to evaluate the resistance of coatings to certain chemicals. In this test, a drop of the test substance is applied to the surface of the coating and left for a defined period of time. The drop is then removed and the remaining coating is examined for visible damage or color changes.
The color drop test is particularly useful when evaluating coatings used in the chemical industry, plant engineering or household appliances. By carrying out this test, we can ensure that your coatings meet the requirements in terms of chemical resistance and durability.
Our experienced and qualified team of experts carries out the color drop test in accordance with DIN EN ISO 2143:2018 with the utmost care and precision.
The filiform corrosion test is a method for evaluating the corrosion resistance of coatings on aluminum surfaces. In this test, a defined number of lines are applied to the coating and these lines are then sprayed with a test liquid. The coating is then examined for visible corrosion damage or blistering.
Filiform corrosion testing is particularly useful when evaluating coatings used in environments exposed to high humidity, salt water or other corrosive environments. By performing this test, we can ensure that your coatings meet the requirements in terms of corrosion resistance and durability.
Our experienced and qualified team of experts carries out filiform corrosion testing in accordance with DIN EN ISO 4623-2/DIN EN 3665 with the utmost care and precision.
In the cross-cut adhesion test, a grid pattern is applied to the coating and then carefully cut into it. An adhesive tape is then applied to the incised surface and then peeled off. The test evaluates the adhesive strength of the coating by counting the number of squares removed from the grid pattern.
The cross-cut adhesion test is particularly useful when evaluating coatings that are exposed to high stress or are applied to surfaces with an uneven texture. By performing this test, we can ensure that your coatings meet the requirements in terms of adhesion and durability.
Our experienced and qualified team of experts carries out the cross-cut adhesion strength test in accordance with DIN EN ISO 2409 with the utmost care and precision.
Gloss measurement is used to determine the gloss level of a surface. The light reflected by the surface is measured and converted into gloss level values. The measurement can be carried out with a gloss meter, which directs the reflected light onto a photocell and shows the measured values on a display.
Gloss measurement is particularly important when assessing paintwork and other surface coatings. A certain gloss level may be required for aesthetic purposes, for example, or serve as an indicator of the quality and durability of the coating.
Our experienced and qualified team of experts carries out gloss measurements in accordance with DIN EN ISO 2813 with the utmost care and precision.
The climate test is an important test that is used to test the weather resistance of coatings and surfaces under different environmental conditions. The test specimens are exposed to various climatic conditions such as humidity, temperature, UV light and salt spray in order to test their resistance.
Climate testing is of particular importance for the automotive industry, where the resistance of aluminum surfaces to various environmental influences such as sunlight, rain, snow and salt is crucial. Climate testing is also of great importance in the construction industry and other sectors in which aluminum and aluminum alloys are frequently used.
Our experienced and qualified team of experts carries out the air conditioning test in accordance with PV 1200, PV 2005-A, PTL 8140, BMW PR 303.5, DBL 5471 and DBL 5416 with the utmost care and precision.
The condensation climate test is an important test for testing the resistance of coatings and surfaces to moisture and condensation. The test specimens are placed in a climate chamber in which they are exposed to alternating periods of high humidity and dryness. This simulates the effects of moisture and condensation in real environments and makes it possible to test the resistance of coatings and surfaces under such conditions.
Condensation climate testing is of particular importance for the automotive industry, where the resistance of aluminum surfaces to moisture and condensation plays an important role. Condensation climate testing is also very important in the construction industry and other sectors in which aluminum and aluminum alloys are frequently used.
Our experienced and qualified team of experts carries out the condensation water climate test in accordance with DIN EN ISO 6270-1 and DIN EN ISO 6270-2 with the utmost care and precision.
Our salt spray test in accordance with DIN EN ISO 9227/ASTM B 117 is a proven method for determining the corrosion resistance of metal surfaces. This involves creating an artificial atmosphere that is exposed to salt spray in order to observe the reaction of the surface to the aggressive environment.
Our state-of-the-art test bench enables us to carry out both standardized and customer-specific tests to meet the individual requirements of our customers. We focus on the highest precision and careful execution to deliver accurate and reliable results. Contact us to find out more about our corrosion testing services.
The scratch resistance test in accordance with DIN EN ISO 1518-1 is an important test for evaluating the surface resistance of coated materials. A defined force is applied to the surface with a steel pin and the resulting scratch mark is then measured. This enables a precise assessment of the scratch resistance and can help to uncover possible weak points in the coating. Our experienced employees carry out the scratch resistance test using state-of-the-art equipment and in accordance with the applicable standards to provide you with meaningful and reliable results. Please contact us to find out more about our testing services.
Our ball impact test in accordance with DIN EN ISO 6272-2 and ASTM D2794 is a proven method for determining the impact resistance of coatings and surfaces. A defined ball is dropped onto the surface to be tested and the degree of damage is measured.
This test method is particularly relevant for components and products that are susceptible to impact or shock in daily use. These include, for example, vehicle parts, electronic devices and furniture. The ball impact test enables a quick and reliable assessment of the impact resistance and therefore the quality of the surface coating.
Our testing equipment meets the latest standards and ensures precise and reproducible results. We can tailor our tests to your individual requirements and also simulate deviating test conditions such as temperature, humidity or air pressure.
If you would like to find out more about our ball impact testing and other surface testing services, please do not hesitate to contact us.
Apparent conductance measurement in accordance with DIN EN ISO 2931 is a proven method for assessing the resistance of surfaces, especially anodized coatings on aluminium. This test is frequently used in industry to quickly determine the quality of compacted anodized coatings.
The conductivity between an electrolyte measuring cell on the anodized layer and the base material (aluminium) is measured when an alternating current is applied. The measurement results provide information on whether the layer has sufficient density and is therefore corrosion-resistant.
Apparent conductance measurement can also detect subtle differences in the surface finish that are not visible to the naked eye;
Our experienced test technicians have extensive knowledge and state-of-the-art measuring equipment to provide you with accurate and reliable results.
Our coating thickness measurement in accordance with DIN EN ISO 2360 / DIN EN ISO 2178 is an important test for determining the thickness of coatings on metals. We use various methods such as magnetic induction, eddy current or ultrasonic measurement methods to provide you with accurate and reliable results.
Coating thickness measurement is an essential step to ensure that the coatings on the metals meet the requirements and provide the necessary protection. With our precise measurements, you can be sure that the coatings have the correct thickness and therefore offer optimum protection against corrosion and wear.
The rapid weathering test is an important method for testing the resistance of coatings to weathering influences such as UV radiation. Special UV lamps in accordance with DIN EN ISO 16474-3 are used, which simulate sunlight and therefore allow the coating to age quickly. Our experienced experts carry out this test under standardized conditions and provide you with precise and meaningful results. Whether you require a single test or longer-term monitoring of your coatings, we are happy to provide you with our expertise and modern testing equipment.
Characterization of the surface properties
Surface properties are the key to the development and optimization of coatings and surfaces. In addition to color measurement and gloss level, layer thicknesses and surface structure are among the decisive properties for evaluating the surface. If a coating or surface exhibits undesirable properties in the field, for example, investigations to characterize the surfaces and coatings such as REM, REM-EDX, white light interference microscope, XRF, etc.
We characterize different properties as required using the following methods, among others:
- Structure and composition of layer systems (SEM)
- Coating thickness determination (metallographic measurements on the SEM, eddy current determination)
- Color and gloss measurement
- Hardness measurement
- Coating adhesion (cross-cut test EN ISO 2409)
- Surface topography and roughness measurements
- Microhardness, instrumented incision
- Tribological tests
- UV resistance (QUV test ASTM G154)
- Corrosion behavior (NSS and ESS according toISO 9227, Kesternich test DIN 50018, automotive coatings VDA 621-41)
- Determination of the sealing quality

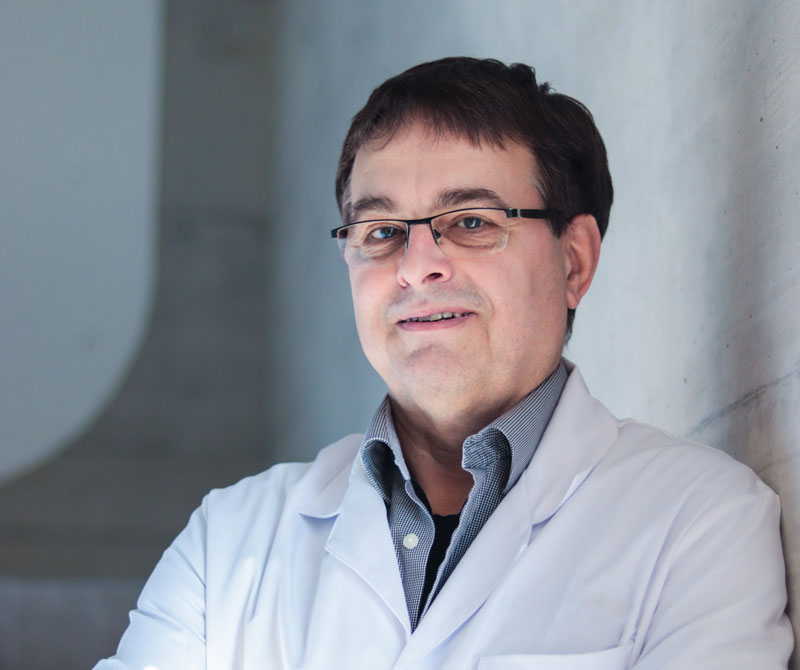
According to standard or customer request,
we analyze.
Call me!