Materials testing
A material test is used to determine material parameters using standardized material samples under mechanical and sometimes also thermal stresses;
The most common destructive test methods include mechanical test methods such as tensile test (yield strength, tensile strength, modulus of elasticity…), compression test, bending test, shear test, torque test, continuous vibration test, continuous bending test but also, for example, for polymer materials thermomechanical analyses such as DSC, DMA, TGA, TMA.
Metallographic investigations also provide further information about the microstructure and thus the behavior of a material.
In addition, we also offer conditional non-destructive testing (e.g. hardness testing, dye penetrant testing, computed tomography examinations). Tests with applied strain gages (strain gauges) are also carried out regularly in our testing laboratory.
Tests to estimate operating loads and the resulting service life of products can be carried out using component tests, fatigue tests for Wöhler curves using standardized material samples. Environmental influences are investigated using various environmental simulations (climate, corrosion, UV…..).
MATERIAL SAFETY THROUGH MATERIAL TESTING
Reliable characteristic values are essential for technically safe products. This is why numerous material tests in our materials testing laboratory are accredited in accordance with ISO/IEC 17025 type C.
Our aim is also to offer competent advice on suitable test methods. This can save a lot of time and money for developments in order to precisely meet the requirements.
The same applies to the interpretation of results. We do not leave anyone alone with the measured values, but interpret and evaluate the characteristic data and analyses of the microstructure for the right decisions!
A broad range of testing methods and analyses are available under one roof . This ensures that, for example, the test engineer can test the components realistically, together with the materials scientist and damage analyst, determine a precise finding about the condition of these components and efficiently process development orders.
In order to reflect reality well, the development of special tests is very often required. We can define and develop these with experience and also carry them out accredited according to ISO/IEC 17025 Type C for special requirements.
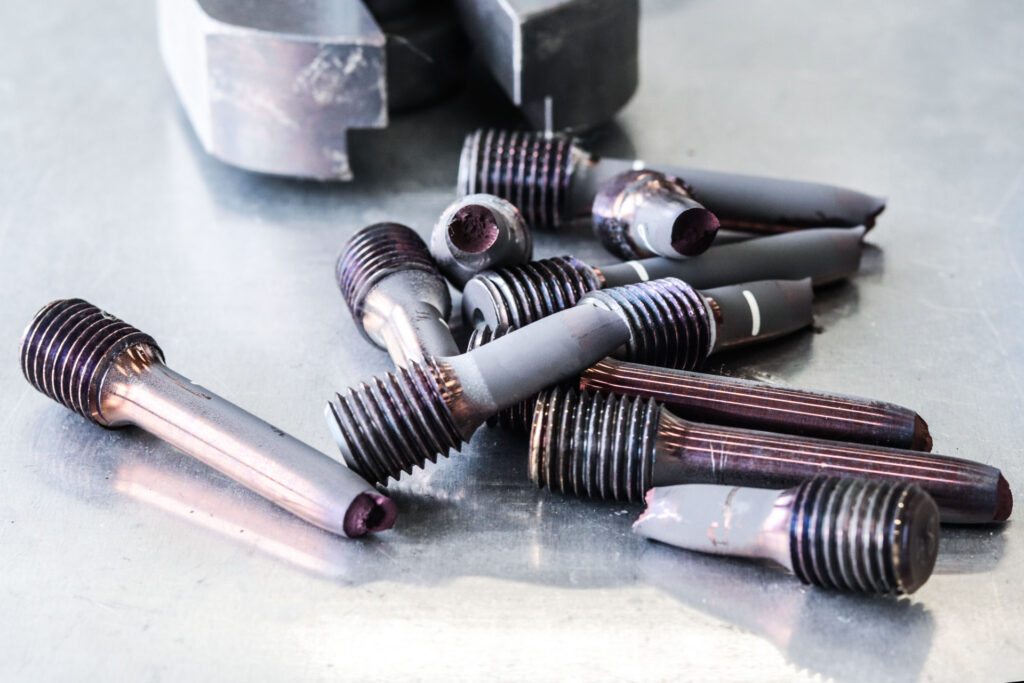
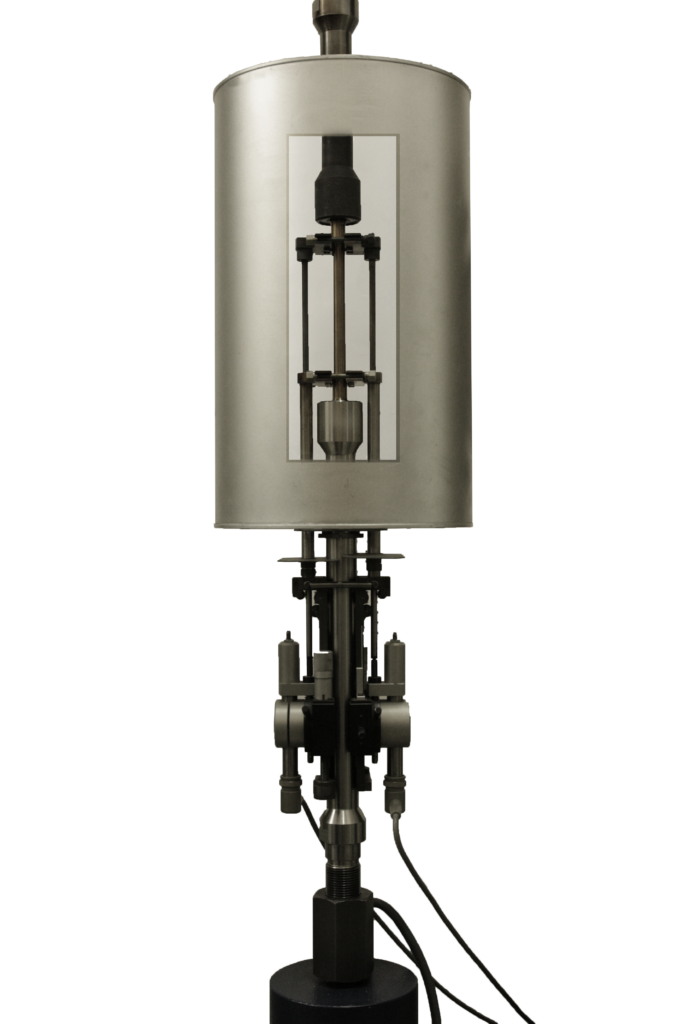
MATERIALS TESTING AND ANALYSIS IN A UNIQUE BANDWIDTH
Our experienced engineers, materials scientists, experts in metallurgy, materialographers, technicians and our chemists in element, polymer and surface analysis ensure a very wide range of materials testing and analysis: mechanical, physical, chemical and microstructural
- Mechanical materials testing: Tensile strength, yield strength, modulus of elasticity, ductility values, strain hardening exponents and perpendicular anisotropy on sheet metal, bending strength, compression tests, hot tensile tests, torque tests, relaxation tests, dynamic tests (LCF, HCF, reverse bending test), special tests
- Metallographic or materialographic investigations: Metallographic grinding preparation of components, semi-finished products or raw materials, investigation of the microstructure, target preparations
- Quality assurance analyses: e.g. grain size determination, alloy composition
- Chemical analyses: Alloy composition (spark OES, XRF), trace elements (wet chemistry, ICP-MS, ICP-OES, AAS), polymer chemistry (FTIR)
- Physical analyses: Thermal analyses, expansion coefficients, corrosion behavior, etc.
- Polymer analytics: Polymer chemistry (FTIR), thermal analyses (DSC, TMA, DMA, melting points, OIT, OOT, crystallinity, TGA), rheological analyses, calorific value determination
EXAMPLES OF WHAT CAN BE READ FROM MATERIAL TESTS FOR SERVICE LIFE BEHAVIOR
- Metallographic or materialographic examinations show segregations, cracks (e.g. hardening cracks), surface layers (e.g. seams, carburization), heat-affected zones in weld seams, cold deformation, type of corrosion or corrosion progression (e.g. liquid metal embrittlement, spongiosis, dezincification), which can have a negative effect on the service life of a component.
- Optimization of heat treatments from a combination of microstructure analyses and mechanical tests
- Quality assurance analyses on semi-finished products (e.g. grain size determination, alloy composition, hardness testing) ensure consistent quality of the starting products